数据驱动的半导体决策转变
半导体生命周期中的数据爆炸
半导体行业一直都是数据密集型的。然而,现在的话题正在从数量转向质量。这不再是关于我们生成了多少数据,而是关于这些数据的连接、情境化和解释程度。
半导体数据与通用的企业或消费者数据有着根本的不同。漏电流读数、故障箱代码或晶圆缺陷没有意义,除非在产生它的硅工艺、测试环境或设计约束的背景下理解它。
在产品开发的早期阶段,设计工程师通过RTL回归、逻辑覆盖率报告和时序收敛检查来生成仿真数据。随着设计进入制造阶段,硅数据开始积累,包括在线计量读数、临界尺寸测量、工具状态日志和晶圆级缺陷图。每个晶圆和批次都带有独特的特征,受上游工艺可变性和工具相互作用的影响。
当产品到达组装和包装时,会出现新形式的数据。材料级应力测试、翘曲分析和热循环行为贡献了直接影响芯片电气特性的附加层。测试数据提供了更清晰的分辨率,提供每个芯片的测量结果、模拟波形和箱分布,从而对性能做出明确的判断。
经常被忽视的是现场和可靠性数据。客户退货、系统内故障或老化趋势可以揭示在鉴定过程中未发现的问题,但前提是这些问题可追溯到原始芯片和测试元数据。这种级别的可见性不仅需要数据收集,还需要跨多个生命周期阶段的上下文深度集成。
当这些信息以碎片形式查看时,它仍然是被动的。然而,当跨设计、制造、测试和现场连接时,借助领域专业知识和时序关联,它成为良率学习、故障分析和运营改进的强大驱动力。
为什么这种数据爆炸很重要以及未来会怎样
从历史上看,许多半导体决策都依赖于工程经验和过去的规范。当流程更简单且产品多样性有限时,这很有效。然而,当今的环境涉及设计、工艺和封装之间的复杂相互作用,通常通过每个晶圆的数百个传感器进行监控,并在多个站点作中进行分析。在这种情况下,仅靠判断力已经不够了。
没有上下文的半导体数据很快就会变成噪音。现在,工程师需要解释来自数千个箱、多种产品变体和不断变化的测试条件的结果。复杂性已经超过了手动跟踪,并且出现细微的系统性故障的风险也增加了。缺陷可能只在极端条件下出现,例如热、电压或极端频率,并且通常只有在将设计、制造和测试的数据汇集在一起时才会显现出来。
现代收益学习依赖于这种集成。确定参数漂移的根本原因可能涉及通过蚀刻步骤均匀性、布局几何形状甚至封装应力进行追溯。产品决策,例如对新代工厂进行鉴定或修改测试内容,现在需要基于历史芯片行为进行仿真和数据建模。这些决策的准确性和速度与数据的连接程度直接相关。
展望未来,数据的作用将变得更加关键。晶圆厂和测试作中的实时调整、基于芯片级特征构建的 AI 辅助诊断以及将现场故障与初始硅批次联系起来的可追溯性框架正在成为标准。目标不仅仅是收集数据,而是创建系统,使决策能够根据可靠的上下文感知洞察不断调整。
工具类型 | 主要目的 |
---|---|
EDA 分析平台 | 分析仿真日志、覆盖差距、布局问题和 IP 重用模式 |
良率管理系统 (YMS) | 检测晶圆级空间缺陷,监控工艺趋势和分箱相关性 |
制造执行系统 | 跟踪晶圆布线、工具偏移、工艺跳过和在线检查日志 |
测试数据分析平台 | 汇总多站点 ATE 结果,识别故障晶粒集群,并规避风险 |
数据湖和管道 | 跨 fab、test 和 reliability 阶段集中结构化/非结构化数据 |
BI 仪表板和统计工具 | 向工程团队展示 KPI 趋势、故障率和良率绩效 |
支持数据驱动流程的工具类型
半导体领域向数据驱动决策的转变之所以成为可能,是因为专业工具类别的不断扩大。这些工具不仅是为了处理数据,也是为了尊重半导体制造的环境,其中每个决策都与晶圆历史、测试条件和物理布局相关联。
与通用企业系统不同,半导体工具必须跟踪全球分布式作中的工艺沿袭、设备行为、批次 ID 和芯片级粒度。结果是一个分层的、高度特定于领域的工具堆栈。
整合仍然是最困难的部分。查看故障晶圆图是一回事,将该图链接到特定的工艺漂移或边际扫描链需要这些工具之间的无缝连接。随着这个生态系统的成熟,目标不再只是收集和显示数据,而是使其在团队和时间范围内可作。
归根结底,任何数据系统的优势不仅在于软件,还在于工程师如何有效地使用它来提出正确的问题并推动更好的结果。
数据驱动半导体时代的技能
随着半导体运营变得更加以数据为中心,成功所需的技能也在不断发展。仅仅成为一个领域的专家已经不够了。工程师和经理现在必须了解如何解释复杂的数据集,并在紧迫的产品和业务时间内对其采取行动。
处理芯片和芯片数据的能力,加上理解数据含义的判断力,正迅速成为跨角色的核心差异化因素。
技能类别 | 描述 | 最重要的地方 |
---|---|---|
数据情境化 | 了解数据的来源以及它如何与流程步骤、设计意图或测试相关联 | 良率分析、硅调试、测试相关性 |
工具熟练程度 | 流畅地使用 JMP、Spotfire、YieldHub、Python、SQL、Excel VBA 或云仪表板等工具 | ATE 调试、故障分析、KPI 报告 |
统计推理 | 应用SPC、分布、假设检验、方差分析、回归模型 | 工艺调整、保护带优化、批次放行标准 |
跨职能思维 | 桥接设计、晶圆厂、测试、封装和现场返回数据 | 汽车、航空航天、高可靠性领域 |
可追溯意识 | 将测试转义或 RMA 与硅历史记录、探针卡更改或封装问题联系起来 | 可靠性、RMA 团队、质量控制 |
决策框架 | 将数据转化为影响业务的见解并确定后续行动的优先级 | 产品和测试经理、项目负责人 |
数据清理和整理 | 检测和纠正异常、格式化原始日志、对齐不一致的源 | ATE 日志分析、晶圆厂工具监控、多批次审查 |
根本原因模式识别 | 识别电气和物理数据层的重复模式 | 故障调试、设备边际分析 |
可视化和报告 | 构建准确总结问题或趋势的仪表板或视觉对象 | 每周产量审查、执行报告、测试计划签核 |
数据治理意识 | 了解共享环境中的数据安全性、版本控制和访问 | 共享供应商生态系统、代工参与 |
AI/ML 熟悉度 | 识别 AI 模型可以在哪些方面协助诊断或决策支持 | 预测性维护、智能分箱、参数化建模 |
这些技能不能替代工程基础知识,而是扩展。一个能够对数据提出更好问题、质疑其质量或将其追溯到正确来源的工程师比仅仅查看图表并继续前进的人更有价值。
随着数据继续成为每个半导体工程判断的核心,理解、塑造和解释这些数据的能力将定义下一代半导体专业人员。
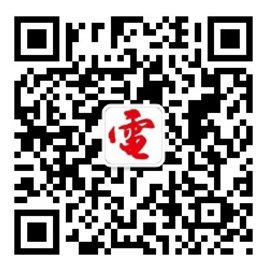
加入微信
获取电子行业最新资讯
搜索微信公众号:EEPW
或用微信扫描左侧二维码