连接未来:构建准确可靠的工厂预测性维护系统
对于工厂的运维管理者而言,确保所有产线的高效稳定长久运行是其核心目标。既要安排好不同产线之间的流水顺序,合理规划物料流转路径,又要尽可能增加每一台工业设备的工作时间,达到更高负荷的运转。但这绝非易事,每一台工业设备,哪怕是同样的批次购买,在同样的时间点投入使用,承载着完全相同的工作负荷,其各自的损耗程度和故障出现频率也不尽相同,无法做到统一管理。
而工厂一旦出现意外停工一次,就会造成巨大的经济损失。来自西门子的一份报告显示,《财富》全球500强中制造和工业企业每年因计划外停机而损失的时间总计达330万小时。据计算因停机而造成的财务成本高达8,640亿美元,相当于其年收入的8%。
图1:由于意外停机造成的损失(图源:西门子)
为了避免意外停机造成的巨大经济损失,就要在设备发生故障之前提前完成维护工作。而依据某一类型号设备划定的一个统一的维护时间安排,落实到每一台设备必然存在一定的冗余量。只是进行这样的计划维护,一方面会增加由于维护带来的计划停机时间;另一方面,又会增加运维人员的工作负担。更关键的是,这种计划之内的过度维护工作,无法预测到不在维护之内的突发状况。
理想的情况是能够针对每一台设备的具体状况,在其即将发生重大故障之前进行维修,甚至可以忽略掉一些并未影响到实际生产的微小故障,持续观察其故障的发展进程,合理安排后续维修时间。由此便可把过度维护中的“冗余量”尽量减少,从而实现每一台设备的更长工作时间,这便是工厂预测性维护的由来。
图2:不同维护方式对比(图源:Microsoft)
工厂预测性维护如何做到精准预测?
当我们提到工厂预测性维护的时候,可以是一个很大的概念,涉及到整个工厂的多条产线,上百台设备的实时监测和维护管理系统;也可以是一个稍小的应用,例如具体到电机的预测性维护解决方案。但不论是大规模的工厂预测性维护系统,还是单一的设备预测性维护方案,工厂预测性维护的实现,本质上是一种基于数据的智能决策过程。它不仅仅依赖于数据采集的精度和算法模型的高效性,还涉及到整个数据生态系统的建设和优化,包括数据的传输、存储、处理和应用。
图3:预测性维护流程(图源:SAP)
提高数据采集精度
在现代预测性维护系统中,通过部署多种传感器,如振动传感器、温度传感器、电流和电压传感器,可以实时监控设备的运行状态。这些传感器能够捕捉到设备的细微变化,例如由轴承磨损或电机故障引起的振动频率改变。
而要注意的是,数据采集的精度不仅仅和传感器本身的参数相关。选择符合特定监测需求和工业环境的高精度传感器只是第一步,而后还有信号处理、校准等一系列具有挑战性的电路设计工作。
模拟信号在传输过程中容易受到噪声和干扰的影响。使用高质量的信号处理芯片(如放大器和ADC转换器)可以确保信号的准确性和稳定性。这些组件负责将传感器捕获的模拟信号转换为数字信号,同时使失真和噪声更小。
为保证数据的准确性,对传感器进行定期校准是必要的。此外,考虑环境因素对传感器性能的影响(如温度变化)并进行相应的补偿,也是确保数据精度的关键。
此外,整个数据采集系统的设计应该考虑到信号的完整性和抗干扰能力,这包括传感器布线、电源管理以及信号的隔离和过滤。
通过这些方法,可以确保从传感器到数据处理系统的每个环节都保持高水平的精度和可靠性,从而为预测性维护提供准确的数据基础。
图4:工厂PdM系统(图源:predicta4)
高效的算法模型
数据本身并不能提供洞见,关键在于如何处理和分析这些数据。在获取到了精准的物理信息之后,机器学习和人工智能技术发挥着重要作用。通过训练算法模型识别正常运行与故障状态之间的差异,可以实现故障的早期检测。例如,通过对历史数据进行学习,算法可以识别特定设备的正常振动模式,并将其与异常模式区分开来。
预测算法的精准度,也可以通过多种途径来提高。
01 定制模型
一方面,可以为特定类型的设备或特定的故障模式定制开发机器学习模型,以提高故障预测的准确性。这包括使用监督学习和非监督学习算法对历史数据进行训练,从而精确识别设备的正常和异常行为模式。
02 集成数据
另一方面,将来自不同传感器的数据集成到一个统一的分析框架中,通过数据融合获得设备状态的更全面视图。同时使用基于物理模型的方法和数据驱动的机器学习模型,通过多模型集成获得更全面的故障预测。再者,建立一个反馈机制,以根据实际维护结果和设备性能数据不断调整和优化预测模型。这涉及到定期重新训练模型,以适应新的操作条件和设备磨损模式。
通过以上技术方法,可以显著提高预测性维护的准确性,从而更有效地预防设备故障和减少停机时间。
可靠的连接实现工厂预测性维护系统的基石
上文探讨了如何提高预测性维护的准确性,而这种准确性的基础是可靠的连接。连接器看似毫不起眼,但在任何一个工业系统中都不可忽视。在保持系统运行稳定性、确保信号传输的可靠性以及方便维护和故障排除方面,连接器起着关键作用。虽然它们不直接参与数据分析或预测算法,但它们的存在对于确保整个预测性维护系统正常运行是必不可少的。
在传感器和数据采集硬件之间必须要有稳定可靠的连接,这样才能确保传感器收集到的模拟信号能够稳定传输到数据采集系统中。而在各种工业控制系统和计算设备之间,如PLC、HMI和服务器等,也需要工业级的连接器来保证数据和控制指令的流通。此外,预测性维护系统中的传感器、控制器和其他一切电子设备的供电,都离不开稳定的电源连接。
图5:工业应用的各类连接器(图源:Samtec)
SEARAY™ SEAM系列是Samtec推出的一款适用于工业场景的高速连接器,提供高达56Gbps的PAM4性能。这款器件在7mm至17.5mm的堆叠高度范围内,可提供多达500个单端I/O,满足高性能和恶劣环境下电子产品的第3类验收标准(IPC J-STD-001F/IPC-A-610F)。
特别值得一提的是,该器件采用了Samtec独有的Edge Rate™触点设计,这一技术专为高速和高频应用的连接器优化性能和耐久性。Edge Rate™技术降低了插拔摩擦力,延长了器件的使用寿命;同时,它还减少了信号损失和串扰,从而显著改善了信号完整性,这对于保证高速信号传输的质量至关重要。有兴趣了解更多信息的用户可以在贸泽电子官网搜索产品编号‘SEAM-40-03.5-S-10-2-A-K-TR’。
图6:Samtec SEARAY™ SEAM系列连接器(图源:Samtec)
另一个给大家推荐的连接器是Samtec的T1M 1mm离散电线端子板。该端子采用磷青铜触点材料和液晶聚合物(LCP)外壳材料制成,额定电流为3.3A,额定电压为250V,工作温度范围为-40°C至+125°C,可以在严苛的工业环境中提供稳定的连接。感兴趣的用户可以前往贸泽电子官网搜索“T1M-05-F-SH-L-K”,获取更多产品信息。
图7:Samtec T1M离散电线端子板(图源:贸泽电子)
预测性维护市场,挑战和机遇并存
根据MarketResearchFuture的一份报告,预测性维护(PdM)市场规模预计将从2022年的218.3亿美元增长至2030年的1113亿美元,复合年增长率(CAGR)为26.20%。市场增长的主要驱动力是降低维护成本的不断增长需求以及实时流分析技术的广泛应用。
图8:PdM市场规模(图源:WOIN)
然而,对于许多工厂来说,部署一个高效的预测性维护系统仍然是一个充满挑战的任务。这一系统的建立需要投资昂贵的传感器、数据存储和分析工具。此外,将预测性维护集成到现有维护流程中可能需要进行重大的组织变革。这意味着员工需要接受新技术的培训,同时管理层也需要理解并支持这种新方法。
但对于工厂管理者而言,这场投入是值得的,因为只有预测性维护才是未来智能工厂所必备的维护策略,这种策略也将支撑现代工业企业持续提高其运营效率和市场竞争力。
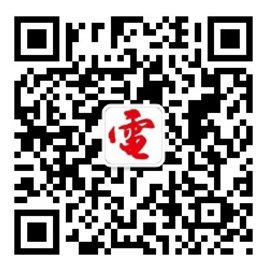
加入微信
获取电子行业最新资讯
搜索微信公众号:EEPW
或用微信扫描左侧二维码