片状多层陶瓷电容机械应力失效分析
编者按:因片式多层陶瓷电容器脆性较强、抗弯曲能力较差,封装尺寸直接影响电器产品使用寿命。组装生产过程中对片状多层陶瓷电容产生应力极易导致贴片电容开裂。本文通过优化电容器选型,更改电容器结构,从根本上杜绝贴片电容机械应力问题。
0 引言
片式多层陶瓷电容器是各电路中重要的电子元器件,因其体积小、电容量范围宽、介质损耗小、稳定性高等优点,被广泛使用在各种电路中。但在使用过程中片式电容器一旦失效将对整体电路造成严重影响。因此需对片式电容的选型、失效机理及材质特性进行深入研究分析。
1 片状多层陶瓷电容简介
片式多层陶瓷电容器是多层叠合结构,相当于多个简单平板电容器的并联体,之所以采用多层结构是为了以较小的体积获取较大的电容量。
多层片式陶瓷电容器的结构主要包括三大部分:陶瓷介质、金属内电极和金属外电极。图1 所示的多层陶瓷电容器是由印好电极(内电极)的陶瓷介质膜片以错位方式叠合起来,经过一次性高温烧结形成陶瓷芯片,再在芯片的两端封上金属层(外电极)制成。
图1 片式陶瓷电容结构图
1.1 失效特性描述
平行电极之间的裂纹主要有两大原因:一是外部机械应力,这种开裂特征基本存在于电极两端,会造成电容器数个平行电极之间开裂。二是电容器制造过程中的工艺缺陷,在电容器非常窄的两个相邻电极之间产生微裂纹,或电容器电极间存在裂缝,电极之间介质开裂,可导电的污染物夹杂其中,介质介电能力下降而发生漏电甚至击穿。
1.2 材质特性
片式多层陶瓷电容通常采用钛酸或钛酸银等陶瓷材料作为电介质,陶瓷材料具有硬脆的物理特性,其塑性形变范围很小,断裂时呈脆性,这使得片式多层陶瓷电容的弯曲形变超过其承受范围时极易产生破裂失效。另外,陶瓷材料耐热冲击性能较差,在环境温度急剧变化或内部受热不均情况下,陶瓷电容也易产生裂纹而失效。
1.3 抗弯曲性
片式多层陶瓷电容能够承受较大的压应力,但抵抗弯曲能力比较差。器件组装过程中任何可能产生弯曲变形的操作都可能导致器件开裂。常见应力源包括:贴片对中工艺过程中电路板操作;流转过程中的人、设备、重力等因素;通孔元器件插入;电路测试、单板分割;电路板安装;电路板定位铆接、螺丝安装等。类裂纹一般起源于器件上下金属化端,沿45°角向器件内部扩展。该类缺陷也是实际发生最多的一种类型缺陷。
2 常见应力失效分析
除了生产过程中出现的失效问题,片式多层陶瓷电容器在装配过程中极易发生应力失效,如运输震动、机械冲击、贴片应力、单边焊料堆积、焊接等。
2.1 PCB板弯曲
PCB 板弯曲导致片式多层陶瓷电容失效如图2所示。
图2 PCB板弯曲导致电容应裂失效
原因分析:在生产组装过程中,避免不了运输、打螺钉、装配,探针测试等,产生PCB 板弯曲应力导致器件破损失效。
2.2 单边焊料过多
单边焊料过多导致片式多层陶瓷电容失效如图3所示。
图3 焊料过多导致电容应裂失效
原因分析:当过程导致焊料堆积,焊锡膏的收缩易导致片式电容器发生断裂。
2.3 吸嘴贴装
吸嘴贴装导致片式多层陶瓷电容失效如图4 所示。
图4 贴装导致电容应裂失效
原因分析:下压压力过大及下压压力过深,导致吸嘴冲击,造成电容破损。
2.4 夹具应力
夹具应力导致片式多层陶瓷电容失效如图5 所示。
图5 夹具应力导致电容应裂失效
原因分析:定位夹具夹力较大时,或因夹具磨损至形状变尖时,会在贴片外部电极处留下划痕,导致内部发生断裂。
2.5 烙铁热量不足
导致片式多层陶瓷电容失效如图6 所示。
图6 烙铁热量不足导致电容应裂失效
原因分析:使用烙铁返修时,如未充分预热,片式电容会因应力导致变形。
2.6 波峰焊预热不足
失效原因分析:因波峰焊接Dip 前预热不足,当片式电容器施加超过允许限度的热应力时,陶瓷外部及内部均会发生断裂。
3 案例分析
故障主板片式多层陶瓷电容器问题突出,分析为主板采用的大封装贴片电容抗弯曲能力较差,故障为片状多层陶瓷电容开裂导致,如图7 所示。结合片式多层陶瓷电容抗弯曲能力差的特点分析研究,并排查生产过程。
图7 故障主板片式电容破裂
3.1 故障失效分析判断
3.1.1 失效机理
根据对故障件的失效分析模式判断,造成电容暗裂的根源是受到来自生产和检验过程中产生的机械应力。
3.1.2 电容抗弯曲能力
根据片式多层陶瓷电容的抗弯曲能力,相关规范中明确1206 及以上封装抗弯曲能力为2 mm,型号越大的电容抗弯曲能力越弱,而此款电容采用的封装为1812。根据前期测试验证数据和售后失效数据统计,1206 及以上型号封装的电容失效故障率相对较高,见图8。
图8 各类封装片式电容失效对比
3.2 过程排查及验证
3.2.1 单体抗弯曲强度试验模拟
从表1 测试数据得出,该片式陶瓷电容器件的重力可以造成器件破损,最小应力在700 ue 以上,与相关标准要求的抗应力指标接近,单体抗弯曲强度、抗应力标准存在波动。
图9 抗弯曲强度模拟实验
3.2.2 过程ICT工装结构排查
目前过程使用此款机型的工装共计设置13根压棒,其中在A 面的失效电容位置(C26 在B 面与之对应的位置:图10 红色区域)也设置了1 根压棒。
3.2.3 过程ICT工装应力测试
在现有工装测试情况下,ICT 应力测试值符合要求,如图11 所示,测试峰值为238 ue,取消该失效电容位置上方的压棒后测试应力峰值为282 ue。
人工设置压棒,并在压棒定点的红色区域移动压棒位置进行验证,两次验证均没有使用一体化工装的应力效果好,验证情况见图12。
第1 次验证在失效电容位置的上方,失效电容应力峰值为577 ue,轻微超出行业标准。
第2 次验证在失效电容位置的左上方,失效电容的应力峰值为637 ue,应力大于第1 次验证。
图10 测试工装排查
图11 ITC应力测试
图12 应力测试数据
3.3 排查验证总结
一体化ICT 工装在测试过程中对失效片状电容产生的机械应力相对较小。验证人工设置压棒的方式由于位置上存在差异,失效片状电容受到的机械应力也有相对差异,同时人工设置压棒存在操作上的不一致性,受到的机械应力相对较大。
故障主板电容型号为1812,型号越大,贴片电容抗弯曲能力越弱,只有从器件选型上去优化,才能完全规避贴片电容破损问题。
相比1206、0805 封装电容,1812 封装器件本体抗机械应力偏弱,个体也存在差异,在过程中存在施加应力导致电容内应力损伤的情况。
3.4 改善方案
3.4.1 ICT 测试工装采用一体化工装,如图13(天板、拖盘、针床一体化),确保测试应力一致性,避免测试下压过程导致贴片受力破损。
图13 TCT改善
3.4.2 将电路进行了优化,将原先的并联改为两个片状电容,从选型上优化并更改为串联,增加冗余设计。有效避免了片状电容破损问题。见图14 和15。
图14 电容并联结构
图15 电容串联结构
3.4.3 如图16 所示, 针对1206 封装片状电容,通过增加电容本体弹性银层提高抗弯曲能力,目前已彻底解决上述片式多层陶瓷电容开裂的问题。
图16 增加弹性银层
4 规避片式多层陶瓷电容断裂建议
通过片式陶瓷电容常见应力损伤案例及分析,为避免封装带来的问题,现提出以下改善建议。
1)如图17 所示,面对压力方向,将零件横向安装,可减缓来自电路板的压力;
图17 模拟纵横向试压
2)无论横竖摆放,片式电容应远离板边;
3)使用小封装电容,减少电容应力故障风险;
4)调整电容布局,使用大封装电容情况下避免近距离并联设计;
5)通过增加电容本体的弹性银层提高抗弯曲能力。
5 结束语
片式多层陶瓷电容因本身脆性特质,在使用中经常出现应力破裂现象,直接影响使用及整体可靠性,本文针对生产过程中的应力对陶瓷电容的影响,结合失效分析研究进行探索。
参考文献:
[1] 吴广霖,白瑞林.片式多层陶瓷电容的可靠性应用研究[J].功能材料与器件学报,2014(5):117-121.
[2] 王玉,贾忠中,刘哲.电子产品组装中陶瓷电容常见失效模式及改善建议[J].电子工艺技术,2018,(3):182-186.
(本文来源于《电子产品世界》杂志2021年11月期)
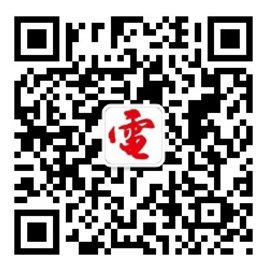
加入微信
获取电子行业最新资讯
搜索微信公众号:EEPW
或用微信扫描左侧二维码